Why You Should Stop Manually Tracking Scaffolding Inventory
Increased construction activity drives a strong scaffolding industry. According to recent research data, the market is worth more than $13 billion and is on track for 5.40% year-over-year growth through 2032.
For scaffolding suppliers, this is great news — if they have inventory management infrastructure in place to meet growing contractor demand.
Put simply, manual tracking isn’t enough. While companies often find this approach cost-effective with small scaffold volumes, as their stock increases and diversifies and contractor requests become more frequent and complicated, it’s easy to lose track of what you have, where you have it, and if it’s available.
Global Site Solutions scaffolding management software offers a way to bridge the gap.
The Hidden Costs of Manual Tracking
Four costs of manual scaffold tracking often hide in plain sight:
Inaccurate Inventory and Material Wastage
Manual tracking can lead to discrepancies between recorded and actual inventory. For example, if scaffolding is returned but not re-entered or sent out but not recorded, totals become unreliable.
This can lead to increased costs as companies either spend on new scaffolding they don’t need or spend time trying to find the cause of the discrepancies.
Higher Project Costs and Delays
Miscounted or missing materials can cause delays. For example, if a miscount leaves you without enough scaffolding to start a new project, you’re stuck waiting for other jobs to finish. Every day you delay drives up the total cost of projects.
Lost Productivity
Manual tracking means manual labor. Staff must take time to record each piece of scaffolding that leaves or enters your warehouse, invest effort in consolidating this data, and ignore other tasks while they address inventory errors.
The result is lost productivity that limits your capacity to take on new work.
Poor Client Experience and Lost Opportunities
If issues with your inventory cause clients to go over time or over budget, the results may be significant. In the best-case scenario, you offer a discount or other benefit to bridge the gap, reducing your revenue. In the worst case, clients end their relationship with your business.
The Benefits of Switching to Scaffolding Management Software
Implementing scaffolding management software can help address and reduce these hidden costs. Key benefits of Global Site Solutions’ Hi-Vis® software include:
Real-Time, Accurate Inventory Control
All inventory is tracked and reported in real time. Staff can view inventory levels on-demand, in turn reducing wastage and increasing accuracy.
Streamlined Project Planning and Scheduling
By integrating inventory data with project schedules, your business can better predict demand and reduce the risk of unexpected delays.
Improved Productivity and Collaboration
With a centralized database, your teams have access to a single source of truth. In practice, this delivers data consistency no matter where, when, or how staff access inventory data. It also enables improved collaboration across projects and locations.
For example, if one project wraps up just as another starts, you can save money and time by moving some (or all) of your inventory from site to site rather than sending it back to your warehouse for manual data entry.
Enhanced Customer Satisfaction
Improved visibility and accuracy mean fewer surprises for your company and your clients, leading to more timely project completion. This increased reliability drives enhanced customer satisfaction, helping your business secure more repeat business and referrals.
Going Up: Building Better Inventory Infrastructure With Global Site Solutions
The costs of manual tracking aren’t immediately obvious, but they are significant. More scaffolding means more complex inventory management, which means a higher risk of costly and time-consuming errors.
With Hi-Vis ®software from Global Site Solutions, your business is better equipped to accurately track and manage scaffold inventory, consistently meet project timelines, and effectively meet customer expectations.
Ready for a better approach to scaffolding management? Start with Global Site Solutions. Let’s talk.
You might also like
GSS Blog
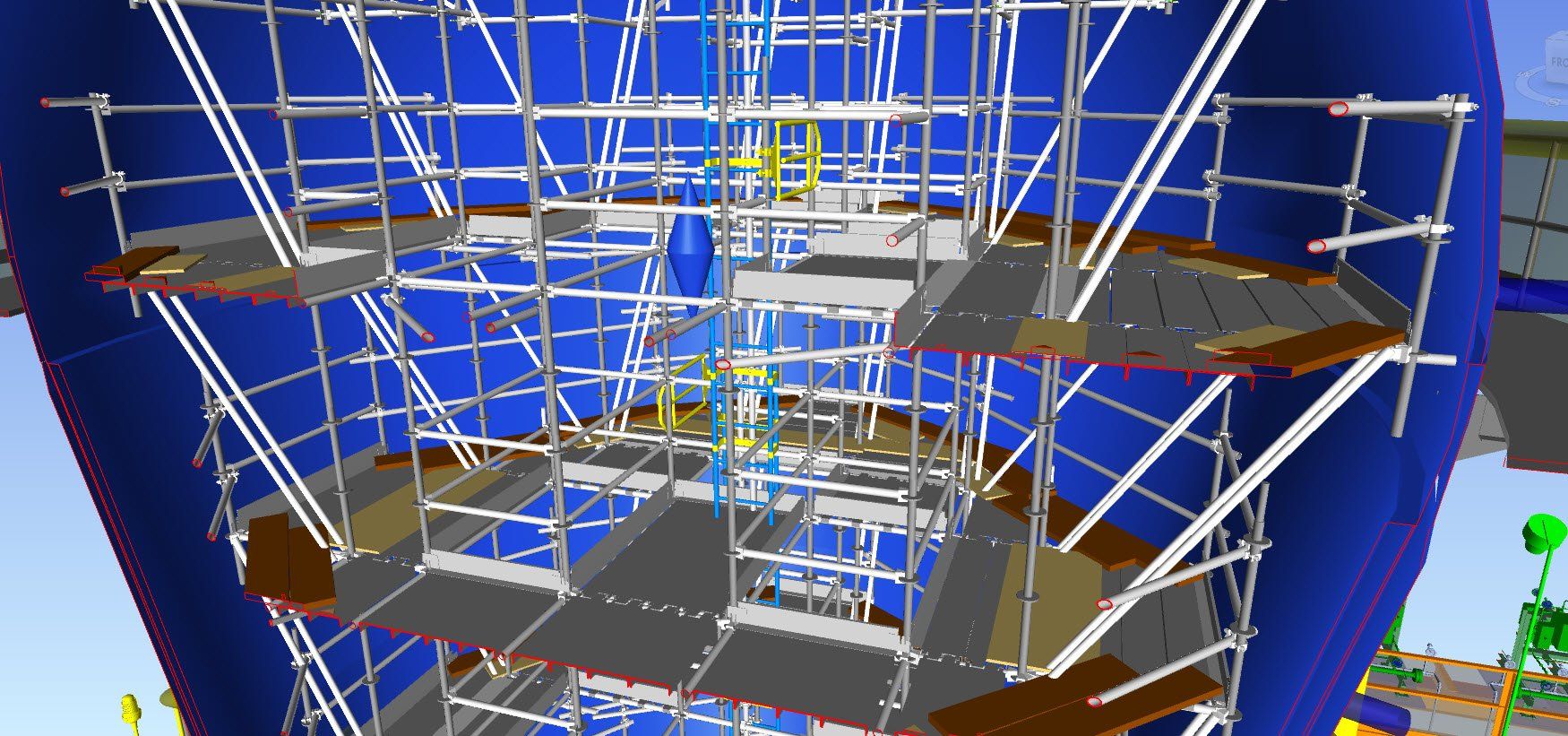
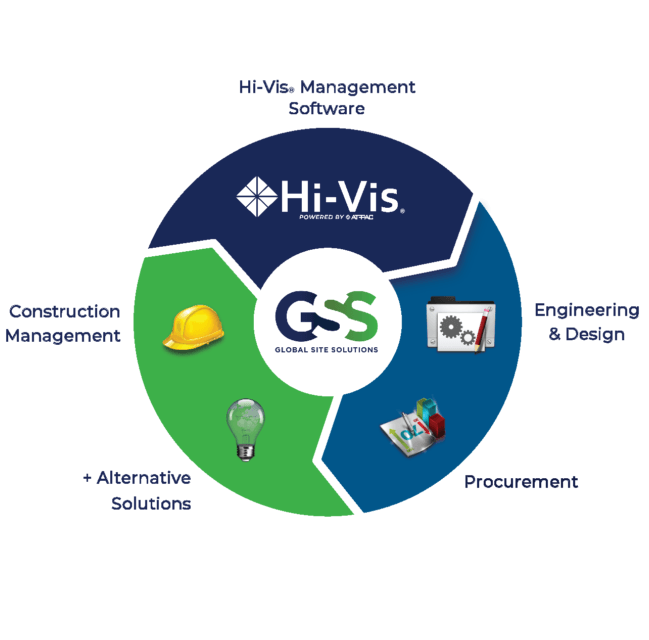
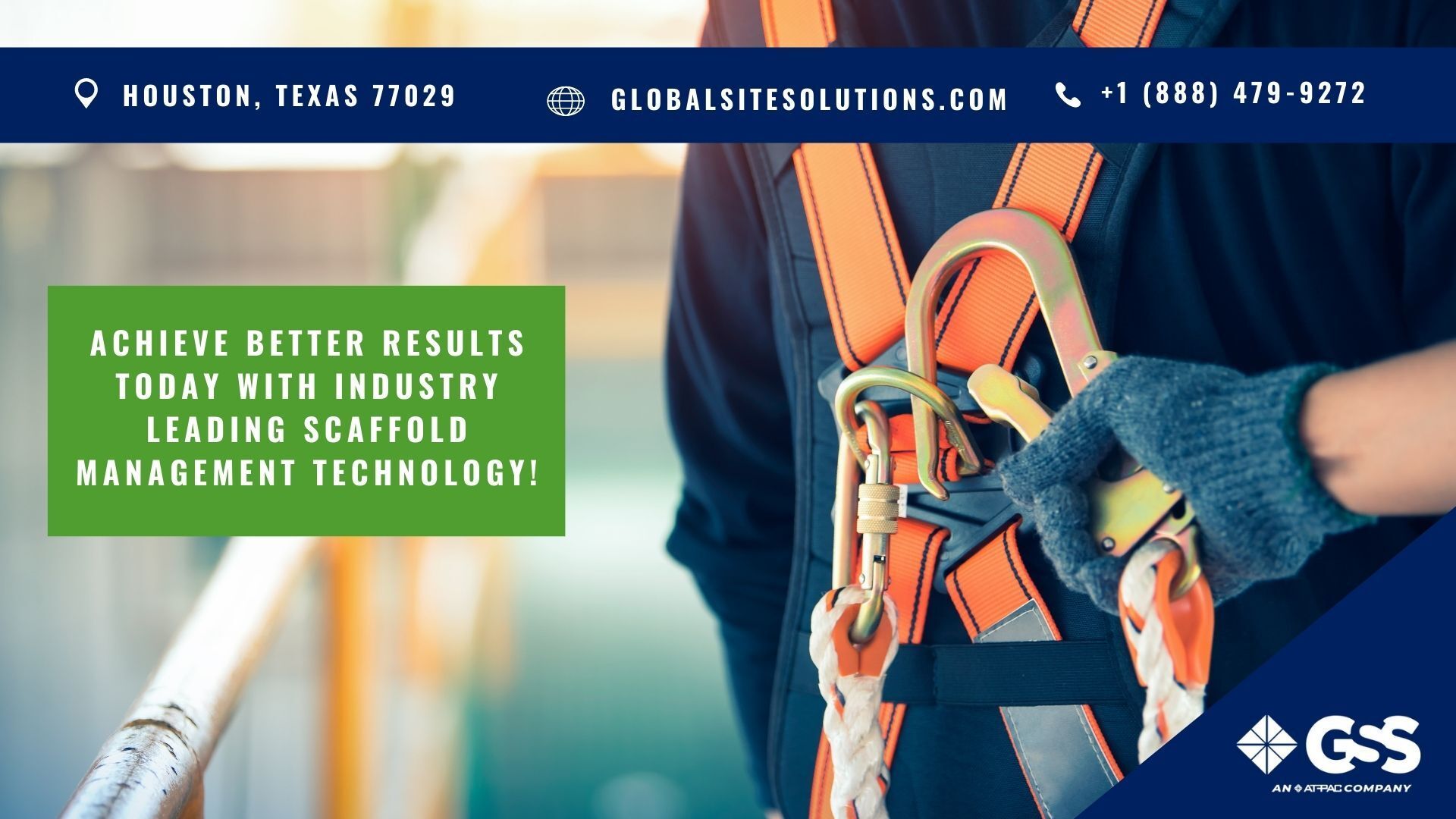
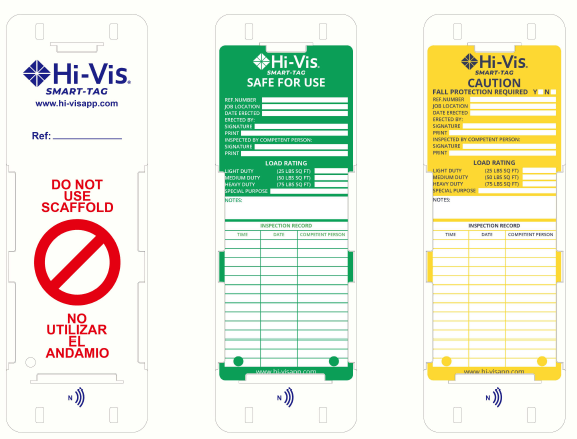